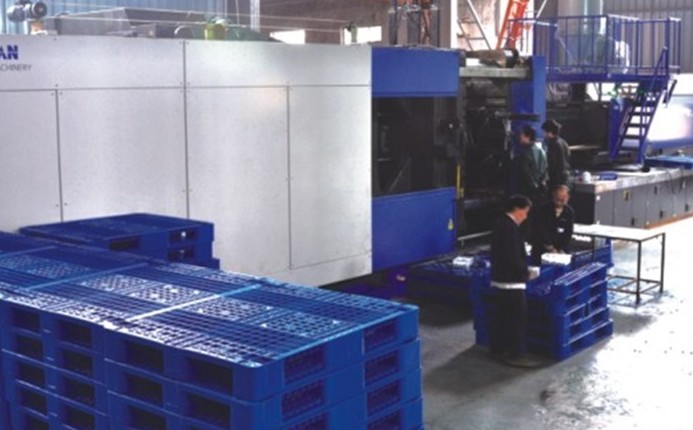
(塑料模具制作和塑料模具材料介绍)
在我们日常的塑料制品产品销售过程中,经常有客户提出能不能重新开模具生产。答案是肯定的,因为塑料制品的产品都会有需要模具来生产,但是现实问题的是,塑料制品模具的制作过程不仅费用庞大,而且来十分的复杂,今天我们来给大家普及一下塑料制品的模具制作的塑料模具材料的相关知识。
塑料模具行业的结构调整在不断的加快,面向市场的专业塑料模具厂家的数量和能力也增长得非常快。根据对塑料模具制造行业的生产、销售、市场情况、行业结构、产品以及进出口等情况分析,参考塑料模具相关行业发展趋势,未来我国塑料模具制造行业的发展空间是非常广阔的。
一、模具制作的前期准备工作
成型塑料制品件的任务书通常由制件设计者提出,其内容如下:
1. 经过审签的正规制制件图纸,并注明采用塑料的牌号、透明度等。
2. 塑料制品件说明书或技术要求。
3. 生产产量。
4. 塑料制品件样品。
通常模具设计任务书由塑料制品件工艺员根据成型塑料制品件的任务书提出,模具设计人员以成型塑料制品件任务书、模具设计任务书为依据来设计模具。
二、 收集、分析、消化原始资料
收集整理有关制件设计、成型工艺、成型设备、机械加工及特殊加工资料,以备设计模具时使用。
1. 消化塑料制品件图,了解制件的用途,分析塑料制件的工艺性,尺寸精度等技术要求。例如塑料制品件在外表形状、颜色透明度、使用性能方面的要求是什么,塑件的几何结构、斜度、嵌件等情况是否合理,熔接痕、缩孔等成型缺陷的允许程度,有无涂装、电镀、胶接、钻孔等后加工。选择塑料制品件尺寸精度最高的尺寸进行分析,看看估计成型公差是否低于塑料制品件的公差,能否成型出合乎要求的塑料制品件来。
此外,还要了解塑料的塑化及成型工艺参数。
2. 消化工艺资料,分析工艺任务书所提出的成型方法、设备型号、材料规格、模具结构类型等要求是否恰当,能否落实。成型材料应当满足塑料制品件的强度要求,具有好的流动性、均匀性和各向同性、热稳定性。根据塑料制件的用途,成型材料应满足染色、镀金属的条件、装饰性能、必要的弹性和塑性、透明性或者相反的反射性能、胶接性或者焊接性等要求。
3. 确定成型方法
采用直压法、铸压法还是注射法。
4、选择成型设备
根据成型设备的种类来进行模具,因此必须熟知各种成型设备的性能、规格、特点。例如对于注射机来说,在规格方面应当了解以下内容:注射容量、锁模压力、注射压力、模具安装尺寸、顶出装置及尺寸、喷嘴孔直径及喷嘴球面半径、浇口套定位圈尺寸、模具最大厚度和最小厚度、模板行程等。
要初步估计模具外形尺寸,判断模具能否在所选的注射机上安装和使用。
5. 具体结构方案
(一)确定模具类型
如压制模(敞开式、半闭合式、闭合式)、铸压模、注射模等。
(二)确定模具类型的主要结构
选择理想的模具结构在于确定必需的成型设备,理想的型腔数,在绝对可靠的条件下能使模具本身的工作满足该塑料制品件的工艺技术和生产经济的要求。对塑料制件的工艺技术要求是要保证塑料制件的几何形状,表面光洁度和尺寸精度。生产经济要求是要使塑料制件的成本低,生产效率高,模具能连续地工作,使用寿命长,节省劳动力。
三、影响模具结构及模具个别系统的因素很多,很复杂:
1. 型腔布置。根据塑件的几何结构特点、尺寸精度要求、批量大小、模具制造难易、模具成本等确定型腔数量及其排列方式。
对于注射模来说,塑料制件精度为3级和3a级,重量为5克,采用硬化浇注系统,型腔数取4-6个;塑料制件为一般精度(4-5级),成型材料为局部结晶材料,型腔数可取16-20个;塑料制件重量为12-16克,型腔数取8-12个;而重量为50-100克的塑料制件,型腔数取4-8个。对于无定型的塑料制件建议型腔数为24-48个,16-32个和6-10个。当再继续增加塑料制件重量时,就很少采用多腔模具。7-9级精度的塑料制品件,最多型腔数较之指出的4-5级精度的塑料增多至50%。
2. 确定分型面。分型面的位置要有利于模具加工,排气、脱模及成型*作,塑料制件的表面质量等。
3. 确定浇注系统(主浇道、分浇道及浇口的形状、位置、大小)和排气系统(排气的方法、排气槽位置、大小)。
4. 选择顶出方式(顶杆、顶管、推板、组合式顶出),决定侧凹处理方法、抽芯方式。
5. 决定冷却、加热方式及加热冷却沟槽的形状、位置、加热元件的安装部位。
6. 根据模具材料、强度计算或者经验数据,确定模具零件厚度及外形尺寸,外形结构及所有连接、定位、导向件位置。
7. 确定主要成型零件,结构件的结构形式。
8. 考虑模具各部分的强度,计算成型零件工作尺寸。
以上这些问题如果解决了,模具的结构形式自然就解决了。这时,就应该着手绘制模具结构草图,为正式绘图作好准备。
四、绘制模具图
要求按照国家制图标准绘制,但是也要求结合本厂标准和国家未规定的工厂习惯画法。
在画模具总装图之前,应绘制工序图,并要符合制件图和工艺资料的要求。由下道工序保证的尺寸,应在图上标写注明"工艺尺寸"字样。如果成型后除了修理毛刺之外,再不进行其他机械加工,那么工序图就与制件图完全相同。在工序图下面最好标出制件编号、名称、材料、材料收缩率、绘图比例等。通常就把工序图画在模具总装图上。
1. 绘制总装结构图
绘制总装图尽量采用1:1的比例,先由型腔开始绘制,主视图与其它视图同时画出。
五、模具总装图应包括以下内容:
1. 模具成型部分结构
2. 浇注系统、排气系统的结构形式。
3. 分型面及分模取件方式。
4. 外形结构及所有连接件,定位、导向件的位置。
5. 标注型腔高度尺寸(不强求,根据需要)及模具总体尺寸。
6. 辅助工具(取件卸模工具,校正工具等)。
7. 按顺序将全部零件序号编出,并且填写明细表。
8. 标注技术要求和使用说明。
六、模具总装图的技术要求内容:
1. 对于模具某些系统的性能要求。例如对顶出系统、滑块抽芯结构的装配要求。
2. 对模具装配工艺的要求。例如模具装配后分型面的贴合面的贴合间隙应不大于0.05mm模具上、下面的平行度要求,并指出由装配决定的尺寸和对该尺寸的要求。
3. 模具使用,装拆方法。
4. 防氧化处理、模具编号、刻字、标记、油封、保管等要求。
5. 有关试模及检验方面的要求。
七、绘制全部零件图
由模具总装图拆画零件图的顺序应为:先内后外,先复杂后简单,先成型零件,后结构零件。
1. 图形要求:一定要按比例画,允许放大或缩小。视图选择合理,投影正确,布置得当。为了使加工专利号易看懂、便于装配,图形尽可能与总装图一致,图形要清晰。
2. 标注尺寸要求统一、集中、有序、完整。标注尺寸的顺序为:先标主要零件尺寸和出模斜度,再标注配合尺寸,然后标注全部尺寸。在非主要零件图上先标注配合尺寸,后标注全部尺寸。
3. 表面粗糙度。把应用最多的一种粗糙度标于图纸右上角,如标注"其余3.2。"其它粗糙度符号在零件各表面分别标出。
4. 其它内容,例如零件名称、模具图号、材料牌号、热处理和硬度要求,表面处理、图形比例、自由尺寸的加工精度、技术说明等都要正确填写。
八、.校对、审图、描图、送晒
A.自我校对的内容是:
1. 模具及其零件与塑件图纸的关系
模具及模具零件的材质、硬度、尺寸精度,结构等是否符合塑件图纸的要求。
2. 塑料制品件方面
塑料料流的流动、缩孔、熔接痕、裂口,脱模斜度等是否影响塑料制件的使用性能、尺寸精度、表面质量等方面的要求。图案设计有无不足,加工是否简单,成型材料的收缩率选用是否正确。
3. 成型设备方面
注射量、注射压力、锁模力够不够,模具的安装、塑料制品件的南芯、脱模有无问题,注射机的喷嘴与哓口套是否正确地接触。
4. 模具结构方面
1). 分型面位置及精加工精度是否满足需要,会不会发生溢料,开模后是否能保证塑料制件留在有顶出装置的模具一边。
2). 脱模方式是否正确,推广杆、推管的大小、位置、数量是否合适,推板会不会被型芯卡住,会不会造成擦伤成型零件。
3). 模具温度调节方面。加热器的功率、数量;冷却介质的流动线路位置、大小、数量是否合适。
4). 处理塑料制件制侧凹的方法,脱侧凹的机构是否恰当,例如斜导柱抽芯机构中的滑块与推杆是否相互干扰。
5). 浇注、排气系统的位置,大小是否恰当。
5. 设计图纸
1). 装配图上各模具零件安置部位是否恰当,表示得是否清楚,有无遗漏
2). 零件图上的零件编号、名称,制作数量、零件内制还是外购的,是标准件还是非标准件,零件配合处理精度、成型塑料制件高精度尺寸处的修正加工及余量,模具零件的材料、热处理、表面处理、表面精加工程度是否标记、叙述清楚。
3). 零件主要零件、成型零件工作尺寸及配合尺寸。尺寸数字应正确无误,不要使生产者换算。
4). 检查全部零件图及总装图的视图位置,投影是否正确,画法是否符合制图国标,有无遗漏尺寸。
6. 校核加工性能
(所有零件的几何结构、视图画法、尺寸标'等是否有利于加工)
7. 复算辅助工具的主要工作尺寸
B.专业校对原则上按设计者自我校对项目进行;但是要侧重于结构原理、工艺性能及*作安全方面。
描图时要先消化图形,按国标要求描绘,填写全部尺寸及技术要求。描后自校并且签字。
C.把描好的底图交设计者校对签字,习惯做法是由工具制造单位有关技术人员审查,会签、检查制造工艺性,然后才可送晒。
D..编写制造工艺卡片
由工具制造单位技术人员编写制造工艺卡片,并且为加工制造做好准备。
在模具零件的制造过程中要加强检验,把检验的重点放在尺寸精度上。模具组装完成后,由检验员根据模具检验表进行检验,主要的是检验模具零件的性能情况是否良好,只有这样才能俚语模具的制造质量。
九、试模及修模
虽然是在选定成型材料、成型设备时,在预想的工艺条件下进行模具设计,但是人们的认识往往是不完善的,因此必须在模具加工完成以后,进行试模试验,看成型的制件质量如何。发现总是以后,进行排除错误性的修模。
塑塑料制品件出现不良现象的种类居多,原因也很复杂,有模具方面的原因,也有工艺条件方面的原因,二者往往交只在一起。在修模前,应当根据塑件出现的不良现象的实际情况,进行细致地分析研究,找出造成塑件缺陷的原因后提出补救方法。因为成型条件容易改变,所以一般的做法是先变更成型条件,当变更成型条件不能解决问题时,才考虑修理模具。
修理模具更应慎重,没有十分把握不可轻举妄动。其原因是一旦变更了模具条件,就不能再作大的改造和恢复原状。
十、整理资料进行归档
模具经试验后,若暂不使用,则应该完全擦除脱模渣滓、灰尘、油污等,涂上黄油或其他防锈油或防锈剂,关到保管场所保管。
把设计模具开始到模具加工成功,检验合格为止,在此期间所产生的技术资料,例如任务书、制件图、技术说明书、模具总装图、模具零件图、底图、模具设计说明书、检验记录表、试模修模记录等,按规定加以系统整理、装订、编号进行归档。这样做似乎很麻烦,但是对以后修理模具,设计新的模具都是很有用处的。
模具??要?
1.一般平板成品不宜中????以防??曲?形。
2.一般情?r下STP在RP正下方。
3.?模座?大?r?STP的?隔??50--200mm。
4.?上下?出板的螺??隔??50--200mm。
5.?有??在滑?K下方或斜梢有靠破?r?上下?出板要?有??制回位?C??。
6.成品拔模斜度以?p??榛?肌?/p>
7.??水路?r??量不要采用水管直接接入模仁?而改用模?水管用"O"RING?接模仁。
8.SP?量?⑵渲?饺〈蟛⒉贾迷诔善返恼?队懊娣e下方。
9.冷?s水路三原?t?A.快速冷?s? B.均?蚰?丞o C.加工方便。
10.斜梢距模具中心??≌??/p>
11.KO孔?注口?套的偏心而偏心?且注口?套的最大?A斜角度不得大于15%%d。
12.?τ诙??肽)o上固定板?母模板之?的分模行程要用?C??加以控制?LP在公模板上必需要有注?бr套?一般?需要有LK??器。
13.?理??鹊广^的方法一般可用斜梢???然?K????板(?出中板)??出梢??M量避免在滑?K底下?以免?生碰撞或干涉。
14.一般模仁超出成品?廓20--30mm,且距模具中心??≌?o模板距模仁?框20--30mm,若有滑?K??急R?⒛0寮哟螬o特?e注意避免和回位梢干涉。
15.支?沃?SP)的?[放???|?距??勘3窒嗟醛o使其模具保持平衡。随着塑料产量的提高和应用领域的扩大,对塑料模具提出了越来越高的要求,促进了塑料模具的不断发展。目前塑料模具正朝着高效率、高精度、高寿命方向发展,推动了塑料模具材料迅速发展。
我国目前用于塑料制品等模具的钢种,可按钢材特性和使用时的热处理状态分类:
1、渗碳型:20,20Cr,20Mn,12CrNi3A,20CrNiMo
2、预硬:Cr2Mo,Y20CrNi3AlMnMo(SM2),5NiSCa,Y55CrNiMnMoV(SM1),4Cr5MoSiVS,8Cr2Mn-WMoVS(8CrMn)
3、调质型:45,50,55,40Cr,40Mn,50Mn,S48C,4Cr5MoSiV,38CrMoAlA
4、耐蚀型:3Cr13,2Cr13,Cr16Ni4Cu3Nb(PCR),1Cr18Ni9,3Cr17Mo,0Cr17Ni4Cu4Nb(74PH)
5、淬硬型:T7A,T8A,T10A,5CrNiMo,9SiCr,9CrWMn,GCr15,3Cr2W8V,Cr12MoV,45Cr2NiMoVSi,6CrNiSiMnMoV(GD)
6、时效硬化型:18Ni140级18Ni170级,,18Ni210级,10Ni3MnCuAl(PMS),18Ni9Co,06Ni16MoVTiAl,25CrNi3MoAl
一、渗碳型塑料模具用钢
渗碳型塑料模具用钢主要用于冷挤压成形的塑料模。为了便于冷挤压成形,这类钢在退火态须有高的塑性和低的变形抗力,因此,对这类钢要求有低的或超低的含碳量,为了提高模具的耐磨性,这类钢在冷挤压成形后一般都进行渗碳和淬回火处理,表面硬度可达58~62HRC。 此类钢国外有专用钢种,如瑞典的8416、美国的P2和P4等。国内常采用工业纯铁(如DT1和DT2)、20、20Cr、12CrNi3A和12Cr2Ni4A钢,以及国内最新研制的冷成形专用钢 0Cr4NiMoV(LJ)。
二、淬硬型塑料模具用钢
(一)常用钢种及热处理
常用的淬硬型 塑料模具钢有: 碳素工具钢 (如T7A、T8A)、低合金冷作模具钢(如9SiCr、9Mn2V、CrWMn、GCr15、7CrSiMnMoV钢)、Cr12型钢(如Cr12MoV钢)、高速钢(如W6Mo5Cr4V2钢)、基体钢和某些 热作模具钢 等。这些钢的最终热处理一般是淬火和低温回火(少数采用中温回火或高温回火),热处理后的硬度通常在45~50HRC以上。
(二)实际应用
碳素工具钢 仅适于制造尺寸不大,受力较小,形状简单以及变形要求不高的塑料模低合金冷作模具钢主要用于制造尺寸较大、形状较复杂和精度较高的塑料模Cr12型钢适于制造要求高耐磨性的大型、复杂和精密的塑料模W6Mo5Cr4V2钢适于制造要求强度高和耐磨性好的塑料模热作模具钢 适合于制造有较高强韧性和一定耐磨性的塑料模。
另外,GD钢也是近年新推广使用的一种淬硬型 塑料模具钢。由于该钢强韧性高、淬透性和耐磨性好,淬火变形小,价格低,用此钢取代Cr12MoV钢或基体钢制造大型、高耐磨、高精度塑料模,不仅降低了成本,而且提高了模具的使用寿命。
三、预硬型塑料模具用钢
所谓预硬钢就是供应时已预先进行了热处理,并使之达到模具使用态硬度。这类钢的特点是在硬度30~40HRC的状态下可以直接进行成形车削、钻孔、铣削、雕刻、精锉等项加工,精加工后可直接交付使用,这就完全避免了热处理变形的影响,从而保证了模具的制造精度。
我国近年研制的预硬化型塑料模具钢,大多数是以中碳钢为基础,加入适量的铬、锰、镍、钼、钒等合金元素制成。为了解决在较高硬度下切削加工难度大的问题,通过向钢中加入硫、钙、铅、硒等元素,以改善切削加工性能,从而制得易切削预硬化钢。有些预硬化钢可以在模具加工成形后进行渗氮处理,在不降低基体使用硬度的前提下使模具的表面硬度和耐磨性显著提高。
四、时效硬化型塑料模具钢
此类钢的共同特点是含碳量低、合金度较高,经高温淬火(固溶处理)后,钢处于软化状态,组织为单一的过饱和固溶体。但是将此固溶体进行时效处理,即加热到某一较低温度并保温一段时间后,固溶体中就会析出细小弥散的金属化合物,从而造成钢的强化和硬化。并且,这一强化过程引起的尺寸、形状变化极小。因此,采用此类钢制造塑料模具时,可在固溶处理后进行模具的机械成形加工,然后通过时效处理,使模具获得使用状态的强度和硬度,这就有效地保证了模具最终尺寸和形状的精度。
此外,此类钢往往采用真空冶炼或电渣重熔,钢的纯净度高,所以镜面抛光性能和光蚀性能良好。这一类钢还可以通过镀铬、渗氮、离子束增强沉积等表面处理方法来提高耐磨性和耐蚀性。
五、耐蚀塑料模具钢PCR
0Cr16Ni4Cu3Nb(PCR)钢属析出硬化 不锈钢 ,硬度为32~35HRC时可进行切削加工。该钢再经460~480℃时效处理后,可获得较好的综合力学性能。
六、其它塑料模具材料
(一)铜合金
用于塑料模材料的铜合金主要是铍青铜,如ZCuBe2、ZCuBe2.4等。一般采用铸造方法制模,不仅成本低,周期短,而且还可制出形状复杂的模具。铍青铜可通过固溶—时效强化,固溶后合金处于软化状态,塑性较好,便于机械加工。经时效处理后,合金的抗拉强度可达1100~1300MPa,硬度可达40~42HRC。铍青铜适用于制造吹塑模、注射模等,以及一些高导热性、高强度和高耐腐蚀性的塑料模。利用铍青铜铸造模具可以复制木纹和皮革纹,可以用样品复制人像或玩具等不规则的成型面。
(二) 铝合金
铝合金 的密度小,熔点低,加工性能和导热性都优于钢,其中铸造铝硅合金还具有优良的铸造性能,因此在有些场合可选用铸造铝合金来制造塑料模具,以缩短制模周期,降低制模成本。常用的铸造铝合金牌号有ZL101等,它适于制造要求高导热率,形状复杂和制造周期短的塑料模具。形变铝合金Lcq也是用于塑料模制造的铝合金之一,由于它的强度比ZL101高,可制作要求强度较高且有良好导热性的塑料模。
(三)锌合金
用于制作塑料模具的锌合金大多为Zn-4Al-3Cu共晶型合金,
模具在工业生产中,用各种压力机和装在压力机上的专用工具,通过压力把金属或非金属材料制出所需形状的零件或制品,这种专用工具统称为模具。
2注塑过程说明编辑模具是一种生产塑料制品的工具。它由几组零件部分构成,这个组合内有成型模腔。注塑时,模具装夹在注塑机上,熔融塑料被注入成型模腔内,并在腔内冷却定型,然后上下模分开,经由顶出系统将制品从模腔顶出离开模具,最后模具再闭合进行下一次注塑,整个注塑过程是循环进行的。
3模具的一般分类编辑(1)非塑胶模具
A.铸造模——水龙头、生铁平台
B.锻造模——汽车身
C.冲压模——计算机面板
D.压铸模——超合金,汽缸体
(2)塑胶模具生产工艺的不同
A.注射成型模——电视机外壳、键盘按钮(应用最普遍)
B.吹气模——饮料瓶
C.压缩成型模——电木开关、科学瓷碗碟
D.转移成型模——集成电路制品
E.挤压成型模——胶水管、塑胶袋
F.热成型模——透明成型包装外壳
G.旋转成型模——软胶洋娃娃玩具
4注塑模具组成编辑(1) 注射成型是塑料加工中最普遍采用的方法。该方法适用于全部热塑性塑料和部分热固性塑料,制得的塑料制品数量之大是其它成型方法望尘莫及的,作为注射成型加工的主要工具之一的注塑模具,在质量精度、制造周期以及注射成型过程中的生产效率等方面水平高低,直接影响产品的质量、产量、成本及产品的更新,同时也决定着企业在市场竞争中的反应能力和速度。
( 2)注塑模具是由若干块钢板配合各种零件组成的,基本分为:
A 成型装置(凹模,凸模)
B 定位装置(导柱,导套)
C 固定装置(工字板,码模坑)
D 冷却系统(运水孔)
E 恒温系统(加热管,发热线)
F 流道系统(唧咀孔,流道槽,流道孔)
G 顶出系统(顶针,顶棍)
5根据浇注系统型制的不同可将模具分为三类编辑(1) 大水口模具:流道及浇口在分模线上,与产品在开模时一起脱模,设计最简单,容易加工,成本较低,所以较多人采用大水口系统作业。
(2) 细水口模具:流道及浇口不在分模线上,一般直接在产品上,所以要设计多一组水口分模线,设计较为复杂,加工较困难,一般要视产品要求而选用细水口系统。
(3) 热流道模具:此类模具结构与细水口大体相同,其最大区别是流道处于一个或多个有恒温的热流道板及热唧嘴里,无冷料脱模,流道及浇口直接在产品上,所以流道不需要脱模,此系统又称为无水口系统,可节省原材料,适用于原材料较贵、制品要求较高的情况,设计及加工困难,模具成本较高。
6塑料模具的发展编辑随着塑料和塑料成型工业的飞速发展,塑料模具也在这时候应运而生,现在对于塑料模具的质量要求也越来越高,这对塑料模具工业的发展提供了巨大的动力。
(塑料模具是塑料制品成型的关键所在)